La pultrusion est une méthode de moulage en continu dans laquelle la fibre de carbone imprégnée de colle traverse le moule pendant le durcissement. Utilisée pour produire des produits aux sections transversales complexes, cette méthode a été réévaluée comme adaptée à la production de masse et à l'amélioration de l'efficacité de production, et son utilisation est en pleine expansion. Cependant, des problèmes tels que le décollement, les fissures, la formation de bulles et des différences de couleur apparaissent souvent à la surface du produit lors de la pultrusion.
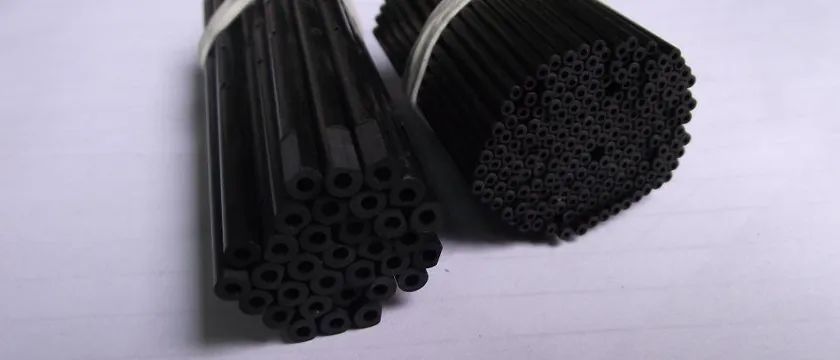
Écaillage
Lorsque des particules de résine durcie sortent du moule à la surface de la pièce, ce phénomène est appelé écaillage ou écaillage.
Solution:
1. Augmenter la température de l'extrémité d'alimentation d'entrée du premier moule de la résine durcie.
2. Réduisez la vitesse de la ligne pour que la résine durcisse plus tôt.
3. Arrêter la ligne pour le nettoyage (30 à 60 secondes).
4. Augmenter la concentration de l’initiateur à basse température.
Cloque
Lorsque des cloques apparaissent à la surface de la pièce.
Solution:
1. Augmenter la température du moule d'entrée pour accélérer le durcissement de la résine
2. Réduisez la vitesse de la ligne, ce qui a le même effet que les mesures ci-dessus
3. Augmenter le niveau de renforcement. Le moussage est souvent causé par des vides résultant d'une faible teneur en fibres de verre.
Fissures de surface
Les fissures de surface sont causées par un retrait excessif.
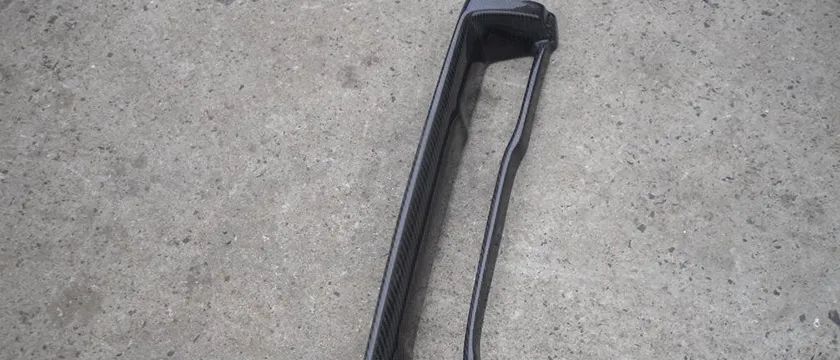
Solution:
1. Augmenter la température du moule pour accélérer la vitesse de durcissement
2. Réduisez la vitesse de la ligne, ce qui a le même effet que les mesures ci-dessus
3. Augmenter la charge ou la teneur en fibres de verre de la charge pour augmenter la ténacité de la surface riche en résine, réduisant ainsi le retrait, les contraintes et les fissures
4. Ajoutez des tampons de surface ou des voiles aux pièces
5. Augmentez la teneur en initiateurs à basse température ou utilisez des initiateurs inférieurs à la température actuelle.
Fissure interne
Les fissures internes sont généralement associées à une section excessivement épaisse et des fissures peuvent apparaître au centre du stratifié ou à la surface.
Solution:
1. Augmenter la température de l'extrémité d'alimentation pour durcir la résine plus tôt
2. Réduisez la température du moule à l'extrémité du moule et utilisez-le comme dissipateur thermique pour réduire le pic exothermique
3. Si la température du moule ne peut pas être modifiée, augmentez la vitesse de la ligne pour réduire la température du contour extérieur de la pièce et le pic exothermique, réduisant ainsi toute contrainte thermique.
4. Réduire le niveau d'initiateurs, en particulier ceux à haute température. C'est la meilleure solution permanente, mais elle nécessite quelques expérimentations pour être efficace.
5. Remplacez l'initiateur à haute température par un initiateur à faible exothermie mais à meilleur effet de durcissement.
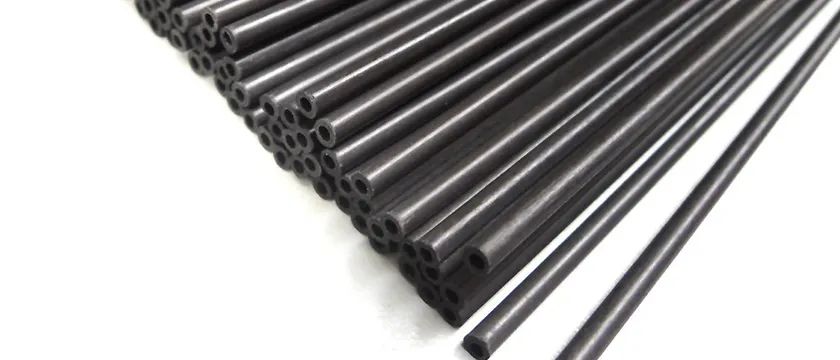
Aberration chromatique
Les points chauds peuvent provoquer un rétrécissement inégal, entraînant une aberration chromatique (également appelée transfert de couleur).
Solution:
1. Vérifiez le chauffage pour vous assurer qu'il est en place afin qu'il n'y ait pas de température inégale sur la matrice
2. Vérifiez le mélange de résine pour vous assurer que les charges et/ou les pigments ne se déposent pas ou ne se séparent pas (différence de couleur)
Faible dureté du bus
Faible dureté Barcol ; due à un durcissement incomplet.
Solution:
1. Réduisez la vitesse de la ligne pour accélérer le durcissement de la résine
2. Augmenter la température du moule pour améliorer la vitesse et le degré de durcissement dans le moule
3. Vérifiez les formulations de mélange qui conduisent à une plastification excessive
4. Vérifiez la présence d'autres contaminants tels que l'eau ou les pigments qui peuvent affecter le taux de durcissement.
Remarque : Les mesures de dureté Barcol ne doivent être utilisées que pour comparer les polymérisations avec une même résine. Elles ne peuvent pas être utilisées pour comparer les polymérisations avec différentes résines, car chaque résine est produite avec ses propres glycols et présente des profondeurs de réticulation différentes.
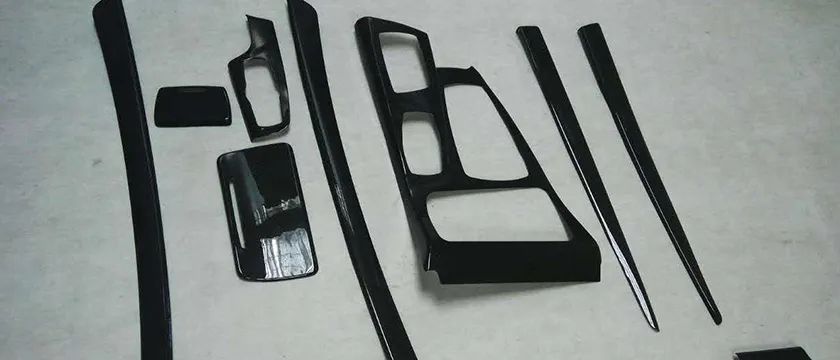
Bulles d'air ou pores
Des bulles d’air ou des pores peuvent apparaître à la surface.
Solution:
1. Vérifiez si l'excès de vapeur d'eau et de solvant est dû au mélange ou à un chauffage inapproprié. L'eau et les solvants bouillent et s'évaporent pendant le processus exothermique, ce qui provoque des bulles ou des pores à la surface.
2. Réduisez la vitesse de la ligne et/ou augmentez la température du moule pour mieux surmonter ce problème en augmentant la dureté de la résine de surface.
3. Utilisez un revêtement de surface ou un feutre. Cela renforcera la résine de surface et aidera à éliminer les bulles d'air et les pores.
4. Ajoutez des tampons de surface ou des voiles aux pièces.
Date de publication : 10 juin 2022